1. 并使颜料在制品中具备更好的分散性
色母生产过程中须对颜料展开细化处置,以提升颜料的分散性和着色力。专用色母的载体与制品的塑料品种相同,具备较好的相匹配性,冷却熔融后颜料颗粒能够较好地集中于制品塑料中。
2. 有助于维持颜料的化学稳定性
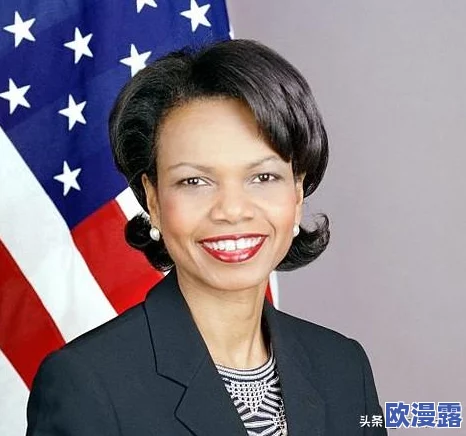
色母就是将颜料与特定的助剂经过特定处置而制取的复合体。在采用过程中,颜料不能轻易碰触空气,因此颜料的化学稳定性以求维持。
3. 确保制品颜色的平衡
色母颗粒与树脂颗粒相似,在计量上更便利精确,混合时不能附着于容器上,与树脂的混合也较光滑,因此可以确保嵌入量的平衡,从而确保制品颜色的平衡。
4. 维护操作方式人员的身心健康
颜料通常就是粉状,嵌入和混合时难舞动,被人体排出后将影响操作方式人员的身心健康。而色母粒在生产过程中经过了处置,有效地减低了颜料对人体的危害。
5. 工序直观,转色难
采用色母可以轻易将颜料压铸或抽走成型,大大简化了生产工序,节省了人力、物力。在须要更改颜色时,只需冲洗注塑机料筒或挤出机即可,无须对设备展开小的改动。
6. 可以节省原材料
色母粒可以根据用户的市场需求展开订制,用户可以挑选自己须要的颜料和助剂,以及相同的载体和浓度,从而可以最大限度地利用原材料,避免浪费。
7. 推动了塑料加工业的发展
色母系列产品的发生,为塑料加工业提供更多了一种高效率、方便快捷、环保的着色解决方案,促进了塑料加工业的发展。它不仅提升了塑料制品的质量和性能,还为塑料加工企业减少了生产成本,提升了生产效率。
色母系列产品的分类
色母系列产品主要存有以下几种分类方法:
1. 按用途分类
- 压铸色母:用作压铸制品的着色,例如家电外壳、汽车零部件等。
- 挤到出众母:用作抽走制品的着色,例如管材、型材、薄膜等。
- 纺丝色母:用作纺丝制品的着色,例如纤维、丝线等。
- 吹塑色母:用作吹塑制品的着色,例如瓶子、容器等。
2. 按载体分类
- PE 色母:以聚乙烯为载体的色母。
- PP 色母:以聚丙烯为载体的色母。
- PS 色母:以聚苯乙烯为载体的色母。
- ABS 色母:以丙烯腈-丁二烯-苯乙烯共聚物为载体的色母。
3. 按颜色分类
- 黑色母:用作黑色塑料制品的着色。
- 白色母:用作白色塑料制品的着色。
- 红色母:用作红色塑料制品的着色。
- 蓝色母:用作蓝色塑料制品的着色。
- 黄色母:用作黄色塑料制品的着色。
色母系列产品的应用领域范围
色母系列产品的应用领域范围非常广为,囊括了塑料、化纤、橡胶等行业。以下就是一些常用的应用领域:
1. 塑料行业
- 压铸制品:例如家电外壳、汽车零部件、玩具等。
- 抽走制品:例如管材、型材、薄膜等。
- 吹塑制品:例如瓶子、容器等。
- 中空制品:例如垃圾桶、周转箱等。
2. 化纤行业
- 涤纶纤维:用作涤纶纤维的着色,例如涤纶长丝、长丝等。
- 锦纶纤维:用作锦纶纤维的着色,例如锦纶长丝、长丝等。
3. 橡胶行业
- 轮胎:用作轮胎的着色,例如胎面、胎侧等。
- 橡胶制品:用作橡胶制品的着色,例如橡胶密封件、橡胶管等。
色母系列产品的挑选和采用方法
1. 挑选最合适的色母系列产品
- 根据塑料制品的用途和建议,挑选最合适的色母系列产品,例如压铸色母、挤到出众母、纺丝色母等。
- 根据塑料制品的材质,挑选最合适的载体和颜料,例如 PE 色母、PP 色母、PS 色母等。
- 根据塑料制品的颜色建议,挑选最合适的颜色,例如黑色、白色、红色、蓝色、黄色等。
2. 采用方法
- 按比例将色母和塑料原料混合光滑,通常建议嵌入量为 2%~5%。
- 采用前要将色母和塑料原料展开潮湿处置,以防止水分对制品质量的影响。
- 压铸或抽走时,应当掌控不好加工温度和时间,以防止颜料水解和制品变色。
- 制品加工顺利完成后,应当展开充份的后处理,例如淬火、淬火等,以提升制品的性能和稳定性。
色母系列产品的发展趋势
随着科技的不断进步和市场需求的不断变化,色母系列产品也在不断发展和技术创新。以下就是一些未来的发展趋势:
1. 环保化
随着环保意识的不断提升,色母系列产品将更加著重环保性能,例如高 VOC、并无重金属等。
2. 功能化
色母系列产品将不断减少功能,例如抗静电、抗菌、工程塑料等,以满足用户相同领域的市场需求。
3. 高性能化
色母系列产品将不断提升性能,例如提升颜料的分散性、耐候性、耐迁移性等,以满足用户制品更高的质量建议。
4. 多功能化
色母系列产品将同时实现多功能一体化,例如将颜料、助剂、功能添加剂等内置在一起,精简生产工艺,提升生产效率。
5. 个性化
色母系列产品将更加著重个性化订制,根据用户的市场需求和建议,提供更多个性化的产品和服务。
色母系列产品就是一种高效率、方便快捷、环保的着色解决方案,广为应用于塑料、化纤、橡胶等行业。随着科技的不断进步和市场需求的不断变化,色母系列产品也在不断发展和技术创新。在未来的发展中,色母系列产品将更加著重环保、功能、高性能、多功能和个性化等方面的发展,为塑料制品的着色提供更多更加优质的产品和服务。